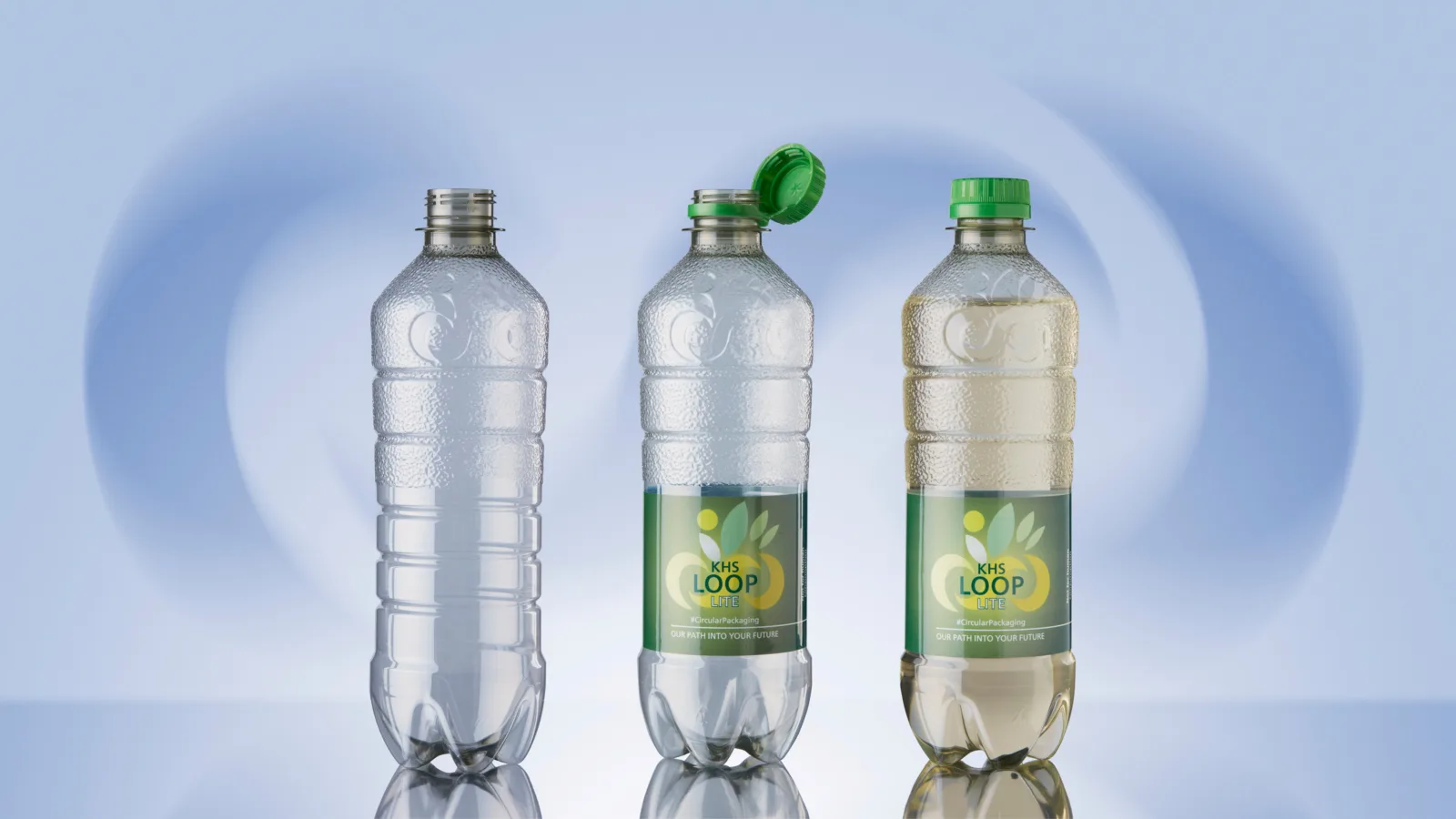
Más rápida, mejor, más ligera
Desde su lanzamiento hace más de 20 años, la protección de producto Plasmax ha sido un caso de éxito. Para que siga siéndolo, KHS invierte en su desarrollo continuo orientado a lograr mayores rendimientos, mayor eficiencia y durabilidad.
En torno a un centenar de máquinas InnoPET Plasmax se encuentran hoy en uso o en proceso de pedido en todo el mundo. Cada año aplican un recubrimiento interior ultrafino, similar al vidrio, a más de 12.000 millones de botellas de PET. La tecnología de barrera de última generación de KHS constituye un caso de éxito único. En su lanzamiento al mercado en 2003, se consideraba todavía una solución innovadora para productos sensibles de nicho que solían envasarse en vidrio. Hoy goza de una aceptación cada vez mayor, en particular entre las embotelladoras multinacionales de bebidas refrescantes carbonatadas. Para ello existen razones de peso.
Empezando, por ejemplo, con el rendimiento de las máquinas de recubrimiento: con una capacidad de 12.000 botellas por hora, esta se ha quintuplicado desde entonces: este año se ha puesto en marcha la primera instalación capaz de producir hasta 60.000 envases por hora. Y esto no acaba aquí, puntualiza Philipp Langhammer, Jefe de Producto de Tecnología de Barrera en KHS: “Seguimos desarrollando continuamente nuestros procesos para alcanzar en el futuro aún mayores rendimientos”.
50 por ciento más de rendimiento
Si bien el proceso, con sus tres etapas y cuatro gases diferentes, es relativamente complejo, cuenta, sin embargo, con más parámetros de ajuste para controlar y acelerar los procedimientos. “En comparación con las soluciones de nuestros competidores, el tiempo de aplicación del recubrimiento no representa un obstáculo. Hemos podido aumentar el rendimiento recientemente hasta en un 50 por ciento en la misma plataforma de 80 cavidades y con un rendimiento de barrera prácticamente idéntico”. En Plasmax no importa el grosor de la capa de óxido de silicio, sino que esta sea completamente uniforme. KHS lo logra con solo unas pocas capas atómicas, que alcanzan un resultado óptimo en un tiempo de proceso muy corto.
Las alternativas de protección de barrera de la competencia, a base de acetileno, requieren capas más gruesas. Su aplicación del recubrimiento lleva comparativamente más tiempo, limitando así el rendimiento. Además, el carbono produce una coloración parduzca de las botellas que no es deseada por muchos fabricantes de bebidas. En cambio, la tecnología de recubrimiento pionera de KHS es totalmente transparente, una ventaja visual tan clara como el vidrio.
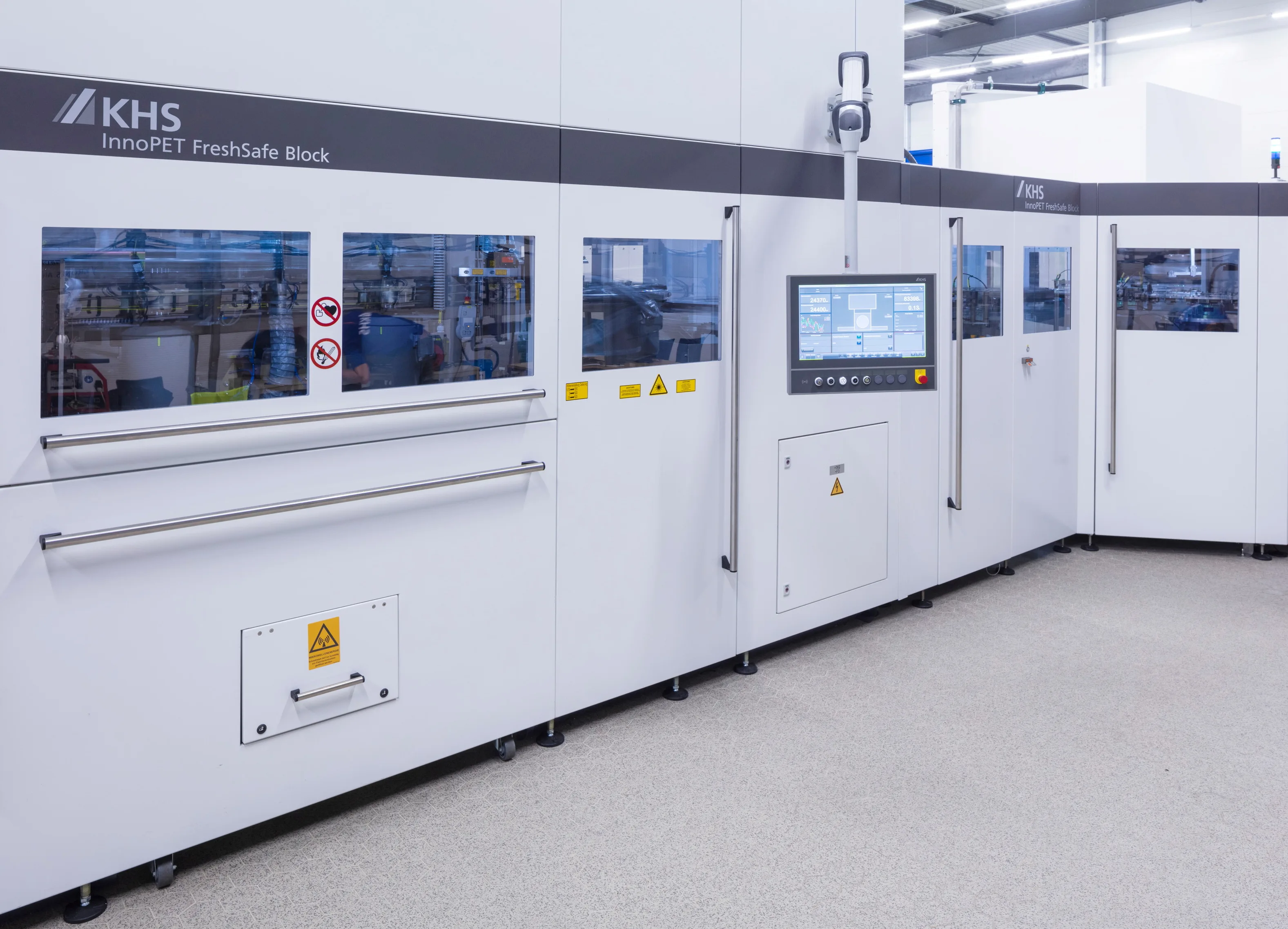
Se utilizan en VILSA-BRUNNEN, en Bruchhausen-Vilsen, Baja Sajonia: la primera máquina Plasmax de última generación, una InnoPET Plasmax 80ER.
Tecnología orientada al TCO
Otro argumento a favor del proceso Plasmax es que, tras el recubrimiento, no quedan partículas sueltas en la botella. Esto hace innecesario el uso de la enjuagadora, indispensable para aclarar los envases en otros sistemas. En este sentido, la tecnología de KHS no solo elimina una máquina, sino que también ahorra recursos como agua y aire.
“Además del mayor rendimiento, este es otro ejemplo de cómo nuestro sistema de protección de barrera sigue un enfoque impulsado por el TCO”, comenta satisfecho Langhammer. En comparación con las botellas multicapa, más complejas de fabricar y más difíciles de reciclar, los costes totales de operación de KHS son solo aproximadamente la mitad.
Menor complejidad
“Además, los mayores intervalos de servicio y de mantenimiento, por ejemplo en las válvulas, también contribuyen al ahorro de costes”, explica Langhammer. “Invertimos de forma continua para reducir la complejidad. Esto incluye, por ejemplo, la eliminación de piezas de desgaste como juntas. Al mismo tiempo, estamos trabajando junto con uno de nuestros proveedores en el desarrollo de bombas autolimpiables, que también permitirán intervalos de servicio más largos”.
“Con Plasmax, KHS actúa aquí como facilitador de formatos de envase pequeños y económicos con la mejor protección posible”.
![]()
Jefe de Producto de Tecnología de Barrera en KHS
Ventaja clave: larga durabilidad
Por supuesto, los costes totales de operación son un factor de gran relevancia para los fabricantes de bebidas, subraya Langhammer. “Pero para nuestros clientes, además de la tecnología, lo más importante es que ofrece una solución de envasado completamente nueva: KHS actúa aquí como facilitador de formatos de envases pequeños y económicos con la mejor protección posible”. Precisamente estos formatos resultan especialmente críticos debido a su relación superficie-volumen: por ejemplo, un refresco en una botella de 200 mililitros sin recubrimiento se conservaría menos de un mes. Particularmente en mercados con veranos secos y calurosos, y picos de demanda estacionales, el suministro resultaría prácticamente imposible.
“Con nuestra tecnología de barrera, actualmente alcanzamos, según las especificaciones, una vida útil de hasta seis meses. Esto permite a las embotelladoras producir con antelación el stock necesario y distribuirlo puntualmente en las regiones donde se demanda. Por un lado, se evitan turnos adicionales en temporada alta. Por otro, gracias a la posibilidad de almacenamiento, una línea de KHS puede producir cada año alrededor de un 30 por ciento más de bebidas que una línea estándar de PET sin recubrimiento”.
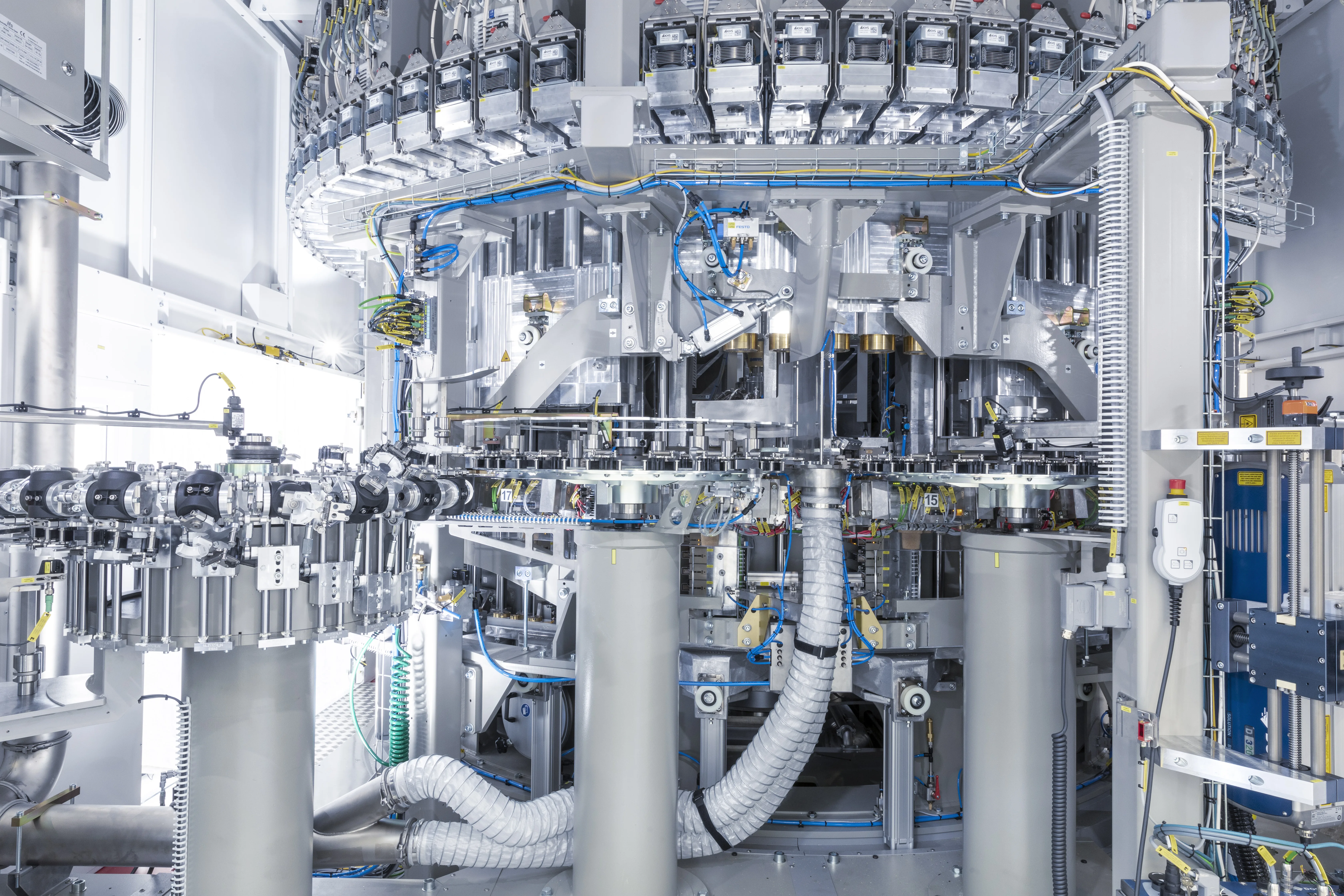
Tras el recubrimiento en el módulo Plasmax, las botellas se giran en una unidad de inversión antes de ser transferidas a la llenadora.
Todoterreno
En el caso de las bebidas refrescantes carbonatadas y el agua, la barrera universal actúa principalmente como una protección pasiva frente a la perdida de CO2. En cambio, en bebidas sensibles como zumos de frutas, bebidas energéticas, tés, vino o cerveza, el objetivo es evitar la entrada de oxígeno en la botella, lo que afectaría negativamente a la calidad del producto.
Para la protección activa, los competidores ofrecen los denominados “scavenger” o aditivos captadores. Se trata de aditivos distribuidos de forma homogénea en el plástico que actúan como protección de barrera. Hoy en día, las botellas con “scavenger” se pueden reciclar con mayor facilidad que los envases multicapa. “Sin embargo, observamos que estos aditivos no se comportan bien con el material reciclado”, señala Langhammer. Esta limitación no existe con Plasmax. Los envases FreshSafe-PET pueden reciclarse de botella a botella, o fabricarse al 100 por cien con rPET. Por eso hablamos de una tecnología de barrera totalmente circular”.
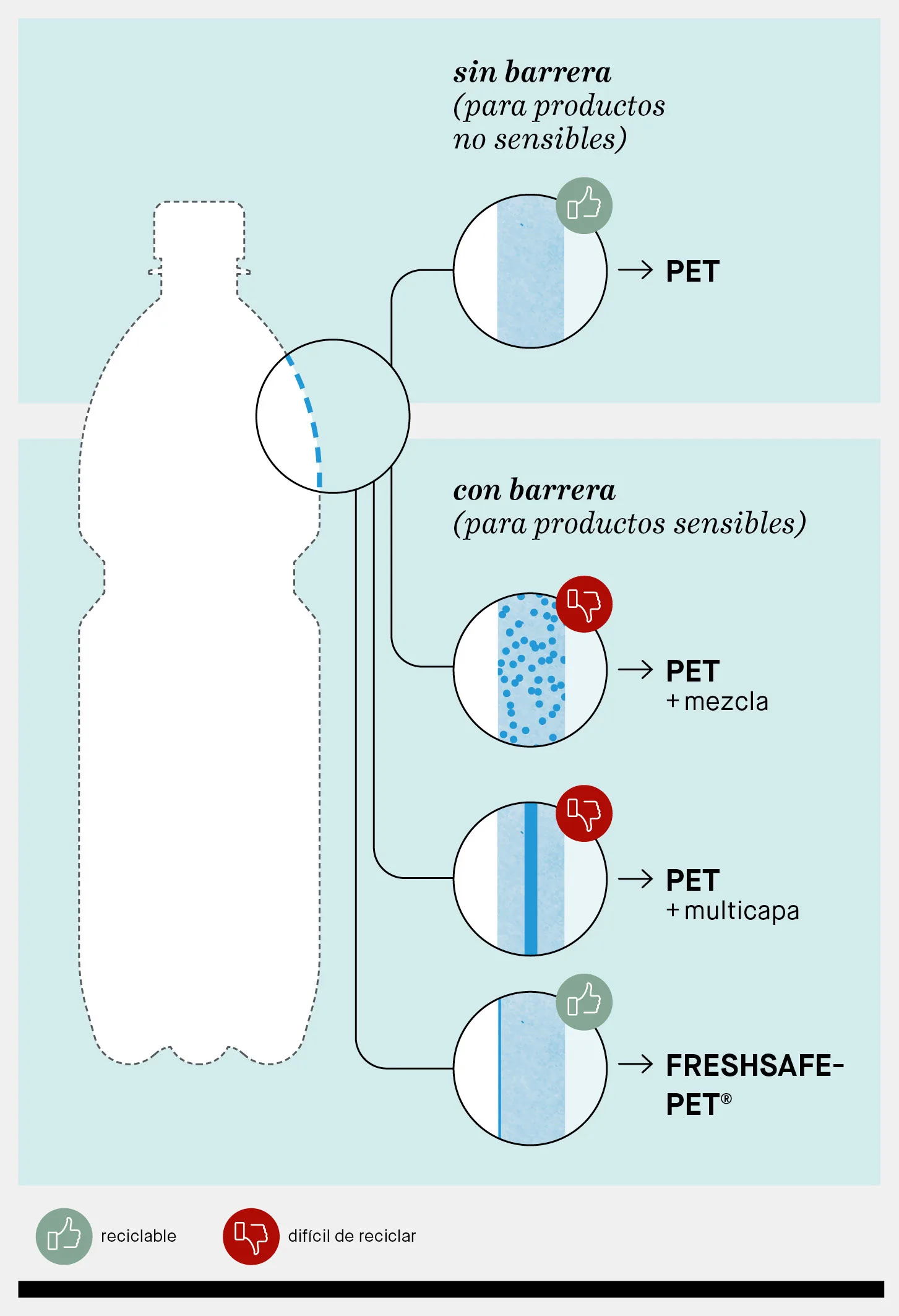
Reciclabilidad – Botellas PET one way: Durante el proceso de reciclaje, las botellas PET sin protección debarrera (para productos no sensibles) suministran un 100% de PET puro.Para botellas de plástico con protección de barrera (para productos sensibles), los aditivos difícilmente pueden separarse del PET, a excepción de FreshSafe-PET®. La capa de protección se elimina sencillamente durante el proceso de reciclado.
Por buen camino
Paralelamente al aumento del rendimiento, la tecnología de KHS se ha seguido desarrollando especialmente en cuanto a su compatibilidad con bloques y líneas: “Con nuestras soluciones en bloque InnoPET FreshSafe estamos completamente integrados en el conjunto de nuestra oferta de productos”, confirma Langhammer. “Plasmax está disponible tanto en configuración en bloque con nuestra máquina de moldeo por estirado-soplado, en la InnoPET FreshSafe Block o en la versión InnoPET FreshSafe TriBlock que además incorpora la llenadora.
Para atender la creciente demanda de su consolidada tecnología de barrera, el proveedor de sistemas con sede en Dortmund ha ido aumentando sucesivamente su capacidad, reduciendo los tiempos de construcción y optimizando el flujo de materiales. De este modo se garantiza que cada año puedan fabricarse aún más máquinas de recubrimiento y bloques FreshSafe. Al fin y al cabo, no queremos que nada se interponga en el camino de nuestra continua historia de éxito”, resume Langhammer.