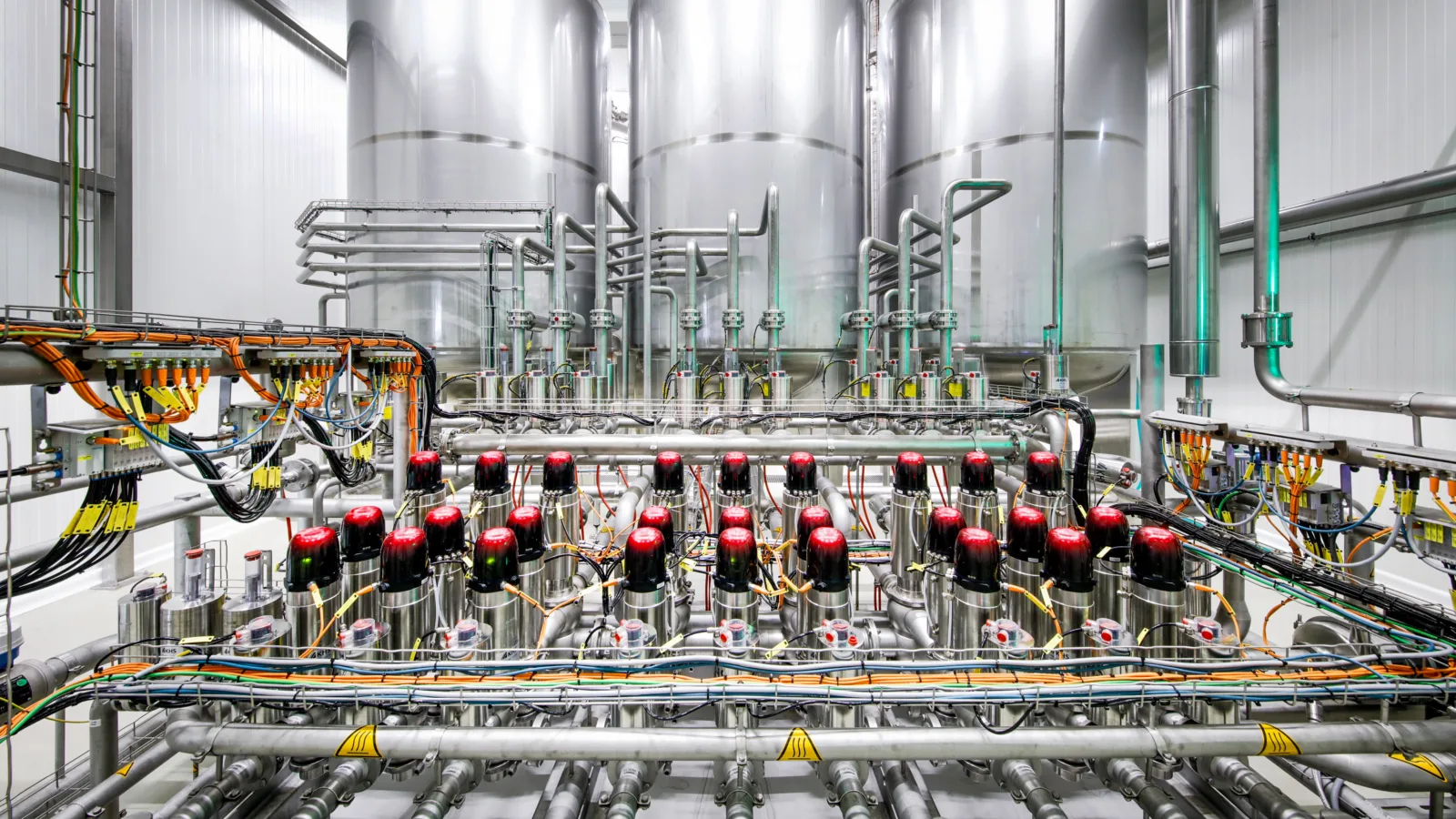
Flexibility first
As the Czech Republic’s most modern contract filler for beverage cans, BOFILLEX leaves nothing to be desired. Thanks to fillers, packers and – first and foremost – process engineering from KHS.
“Until recently, there was only one single commercial filling plant for beverage cans in the whole of the Czech Republic – and this had outmoded technology, low capacities and long wait times,” remembers Tomáš Zahálka, managing director of BOFILLEX in Sokolov near Karlovy Vary, established in 2022. “Key beverage producers thus had to have their products filled in neighboring states such as Poland or Austria.”
Customer and investor
One of these is BIG SHOCK!, whose brand of the same name consumers associate with the most popular energy drinks in the country. With his business concept for a completely new, state-of-the-art filling plant, Zahálka found himself knocking on open doors at the family enterprise. They had long considered creating their own capacities; BIG SHOCK! therefore not only became BOFILLEX’ first and biggest customer but also its investor and principal owner.
With up to eight standard flavors and two to three special editions each year, BIG SHOCK! has something for everyone. It also sells iced tea and coffee and has plenty of other ideas for future product launches in the pipeline.
BOFILLEX’ declared objective is to become a major contract filler for Central Europe. “Although we’ve only been in production since February 2024, we not only work with regional beverage producers and local breweries,” explains Zahálka. “We’ve also already gained customers from other countries in Europe and even outside it. We’re very proud of this fact.”
The first stage in the project involved installing and commissioning a KHS line with a maximum capacity of 26,000 250- and 330-milliliter and 20,000 500- and 568-milliliter cans per hour, with the filling technology of the Innofill Can C forming the heart of the line.
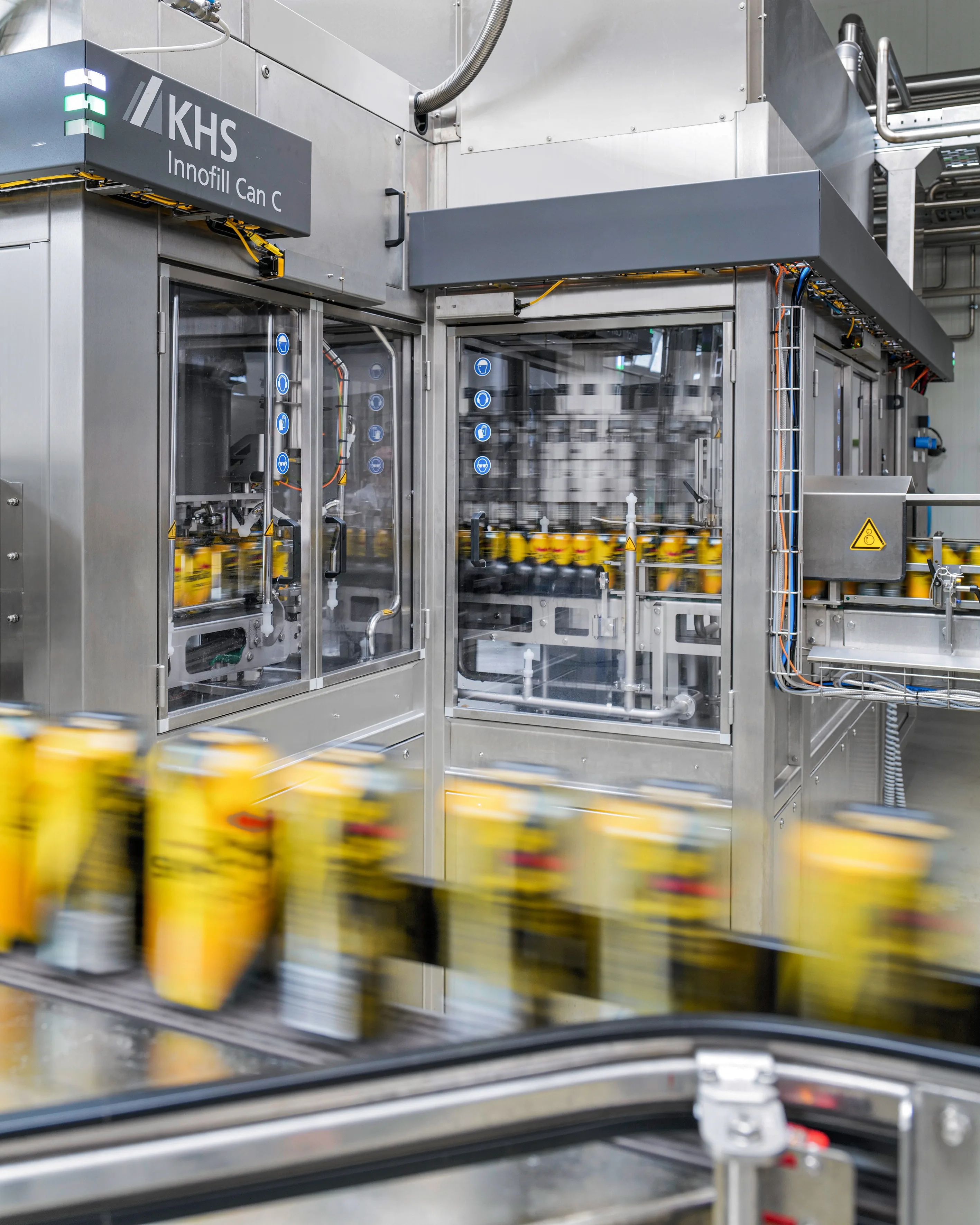
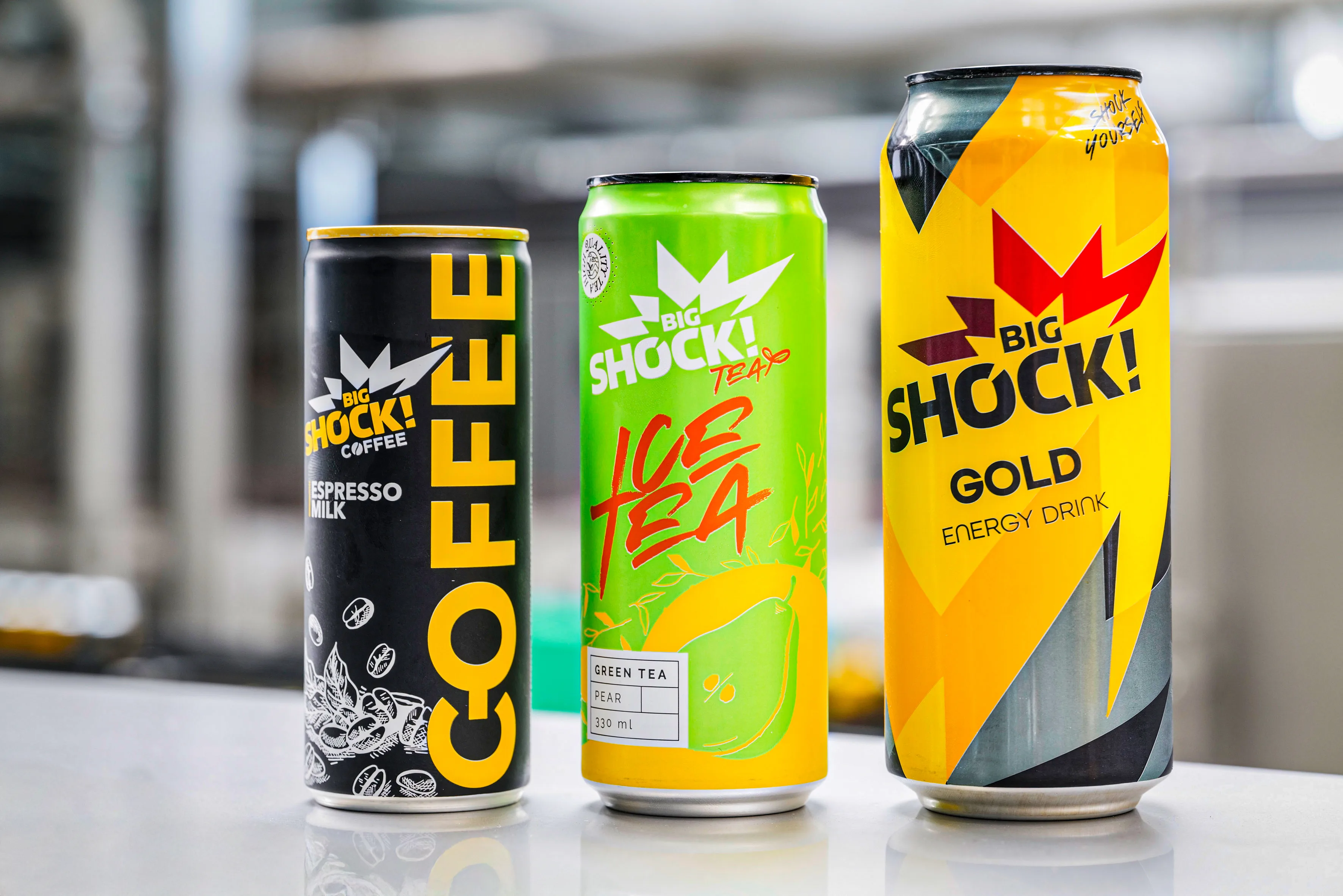
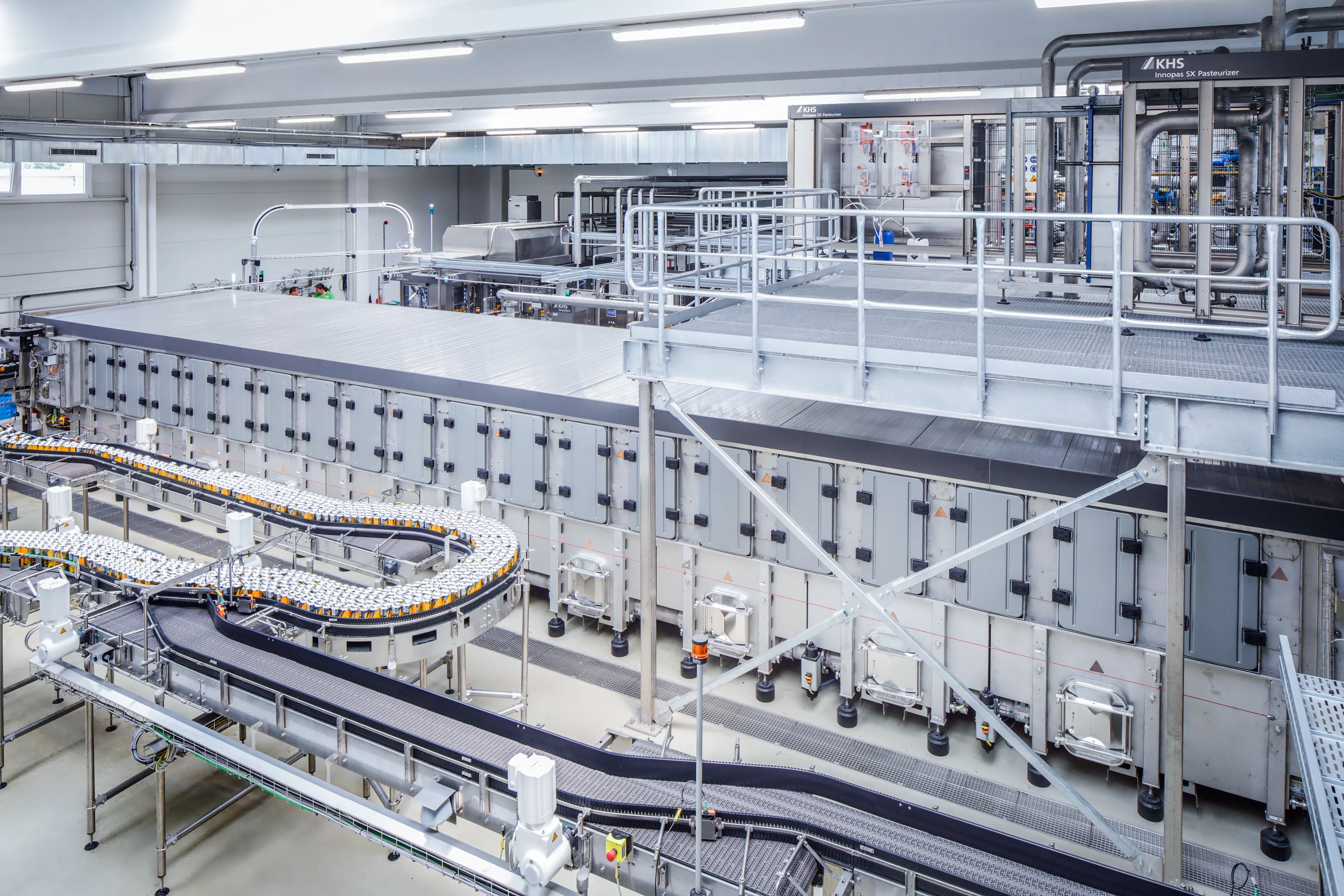
There isn’t just a varied number of container sizes – the vast range of energy drinks, coffee beverages and beer also demands high levels of flexibility.
One-stop technology
The decision to award the Dortmund systems supplier the contract was an easy one for Zahálka. “Right from the start, we were clear that we’d only opt for the technological partner with the best quality and wanted our entire plant to come from a one-stop shop. KHS’ Czech office in Budweis reacted quickly to our request and was very supportive and flexible regarding our wishes and requirements.”
“Right from the start, we wanted to opt for the technological partner with the best quality and procure our entire plant from a one-stop shop.”
![]()
managing director, BOFILLEX
Sales argument packaging
Indeed, flexibility is especially important to BOFILLEX. “In a saturated market it’s the packaging that sells,” Zahálka is convinced. “This is why we have to offer our customers lots of different packaging variants that meet their respective requirements.” The company’s two Innopack Kisters packers produce packs of four and six containers, packaging for individual cans and trays of twelve and 24 with individually printed film.
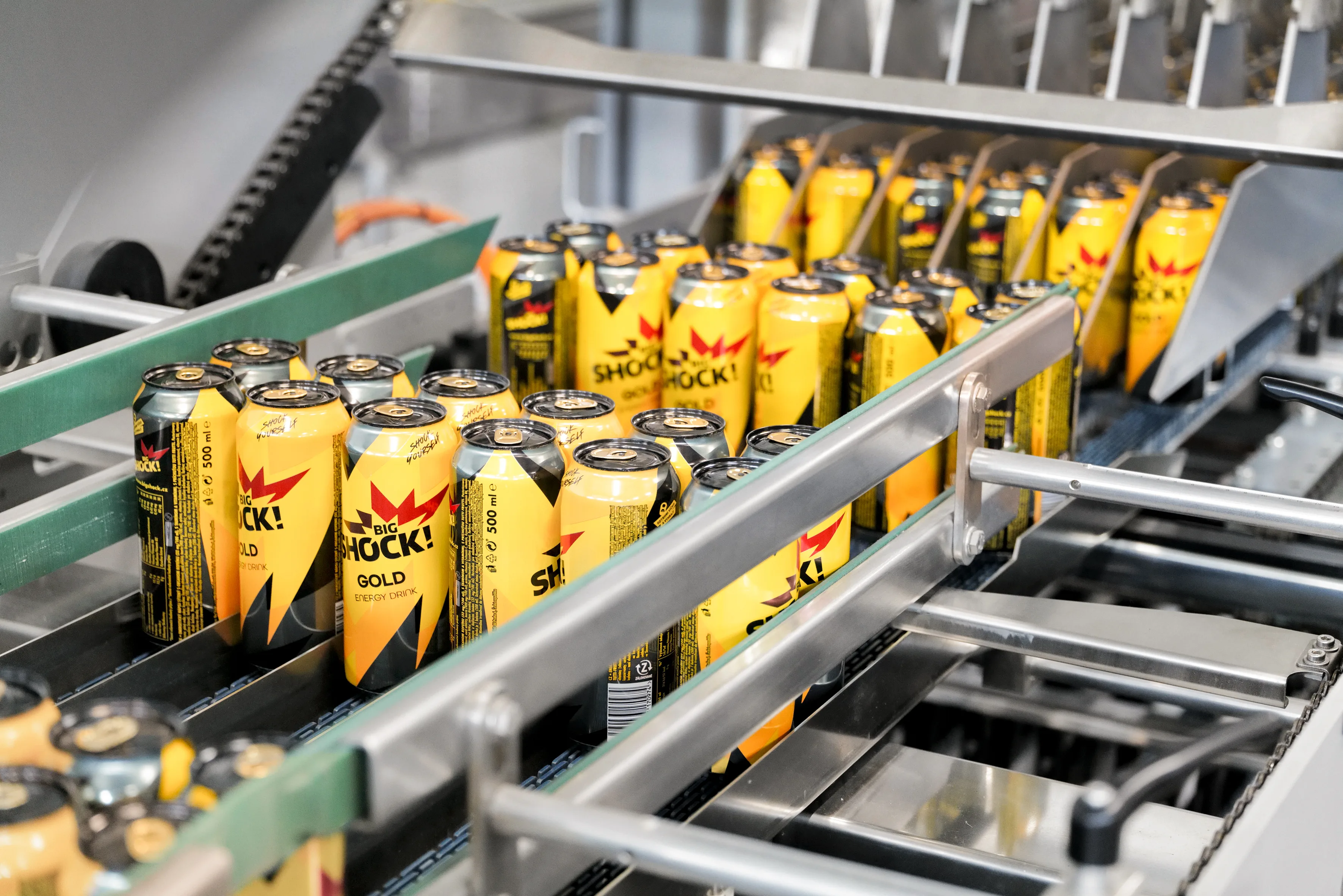
In addition to 4- and 6-packs plus packaging for individual cans, trays complement the varied range of options that BOFILLEX offers to meet its customers’ needs.
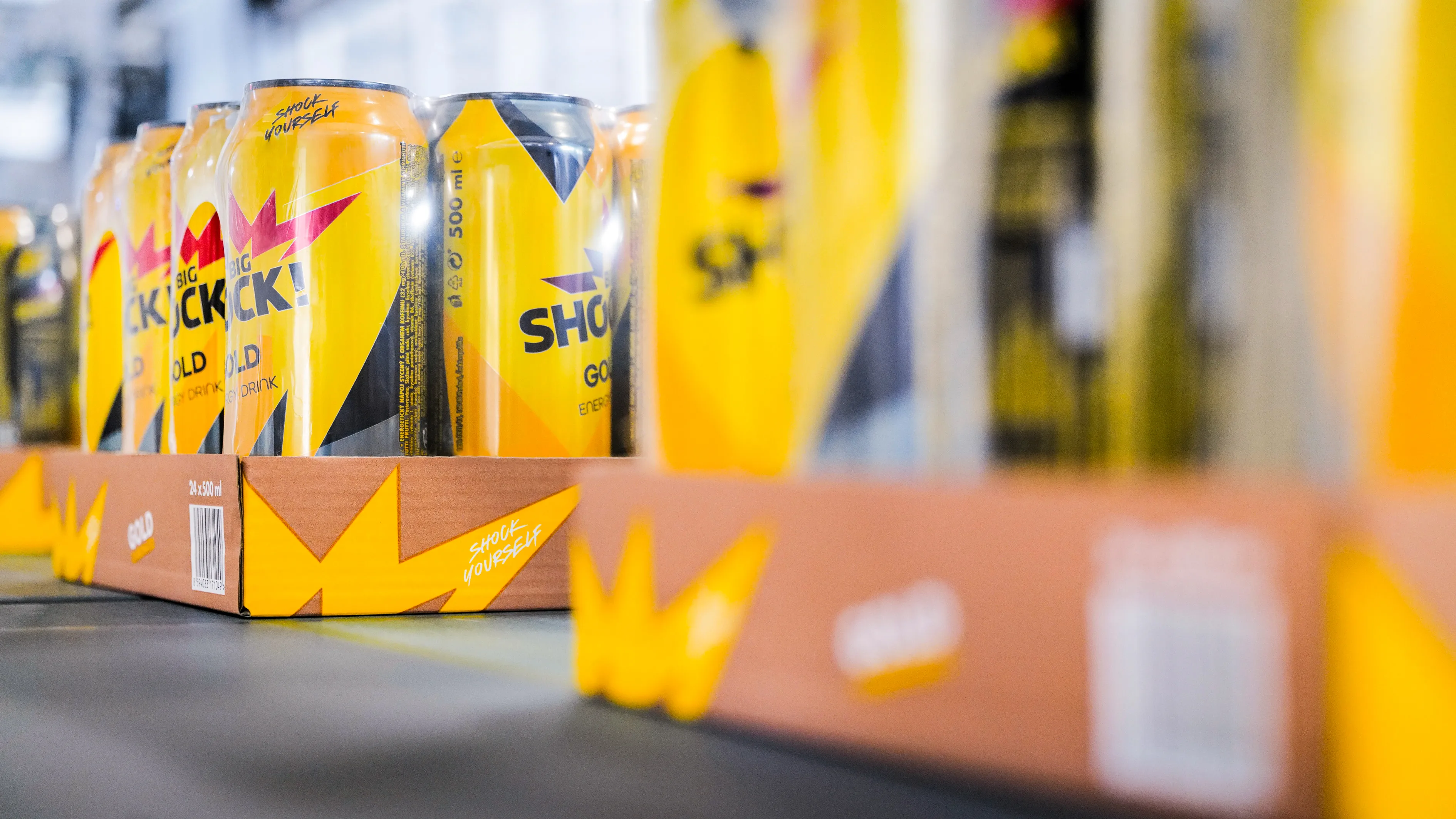
One of two KHS packers is the Innopack Kisters TSP.
Sophisticated process technology
In addition to filling and packaging, BOFILLEX’ main activity is the production of the actual beverages. KHS has installed a multifunctional syrup room for this purpose that can cater for the full product range, however varied. It can make carbonated soft drinks and energy drinks plus mixed beer beverages, for instance. “Our turnkey system scores with absolute accuracy, good tracking and economical media consumption,” emphasizes Lubomir Neubauer, area sales manager for the Czech Republic and Slovakia at KHS.
Two-tank liquid sugar setup
The basis for these products is finished syrup. One key ingredient here is liquid sugar that is continuously produced by the KHS Innopro Delta Jet at a rate of six cubic meters an hour. To this end, the setup features two batch dissolving tanks that operate alternately. The heat recovered from the hot sugar syrup that reaches temperatures of up to 85°C in the one tank preheats the dissolving water in the second. The cooling tower and cold water then cool the liquid sugar down to processing temperature.
Precise dosing
The finished syrups themselves are produced in three 5,500-liter mixing tanks. The main ingredient fed in here besides the liquid sugar is of course water. This makes it easier to process mixed phases and ensures that the required concentration is reached.
Depending on the beverage, various other components are added from a container dispatch station and from an Innopro Batchmix system. The former ensures precisely dosed extraction and supply of liquid ingredients to the mixing tanks. Two separate container connections facilitate fast changeovers. With the help of the latter, the Innopro Batchmix dosing system from KHS, solid and liquid components can be fed in. Once these have been dissolved and mixed in preheated water in two 450-liter tanks, they are fully transferred to the large mixing tanks. This ensures that the finished syrup is of the exact composition required.
Hygiene writ large
In the KHS Innopro Paramix C two-component mixing system the finished syrup is then added to beer or deaerated water to produce the finished product and carbonated if required. The beer needed is stored in a tank farm consisting of nine 10.5-cubic meter bright beer tanks and fully automated valve manifolds that is supplied by a truck acceptance panel. Hygiene and low operator involvement are writ large here.
Media is fed in on the one side of the syrup room, with operation and logistics clearly separated on the other. All told, the process technology in this area has been designed as a semiautomatic system. Coupling panels are used to switch the setup over from cleaning to mixing.
“Our syrup room scores with absolute accuracy, good tracking and economical media consumption.”
![]()
area sales manager for the Czech Republic and Slovakia, KHS
Safe beverage production
The entire syrup room is regulated by a process control system that stores and redundantly archives all process-relevant data. Batches can be tracked for each order using connected hand scanners. As the warehouse is also linked into the system, the same goes for the origin of the raw materials and the quality of the finished products.
BOFILLEX has invested a total of about €15 million in its first line. The chosen site is excellently located and easily reached by road and rail. The most important criterion, however, was that there is room for further expansion. “We believe in the beverage can and are convinced that this beverage container will continue to grow even more,” says Zahálka, looking optimistically into the future. “This is why we’re planning on already investing in a second, even more powerful filling line at the beginning of next year.”