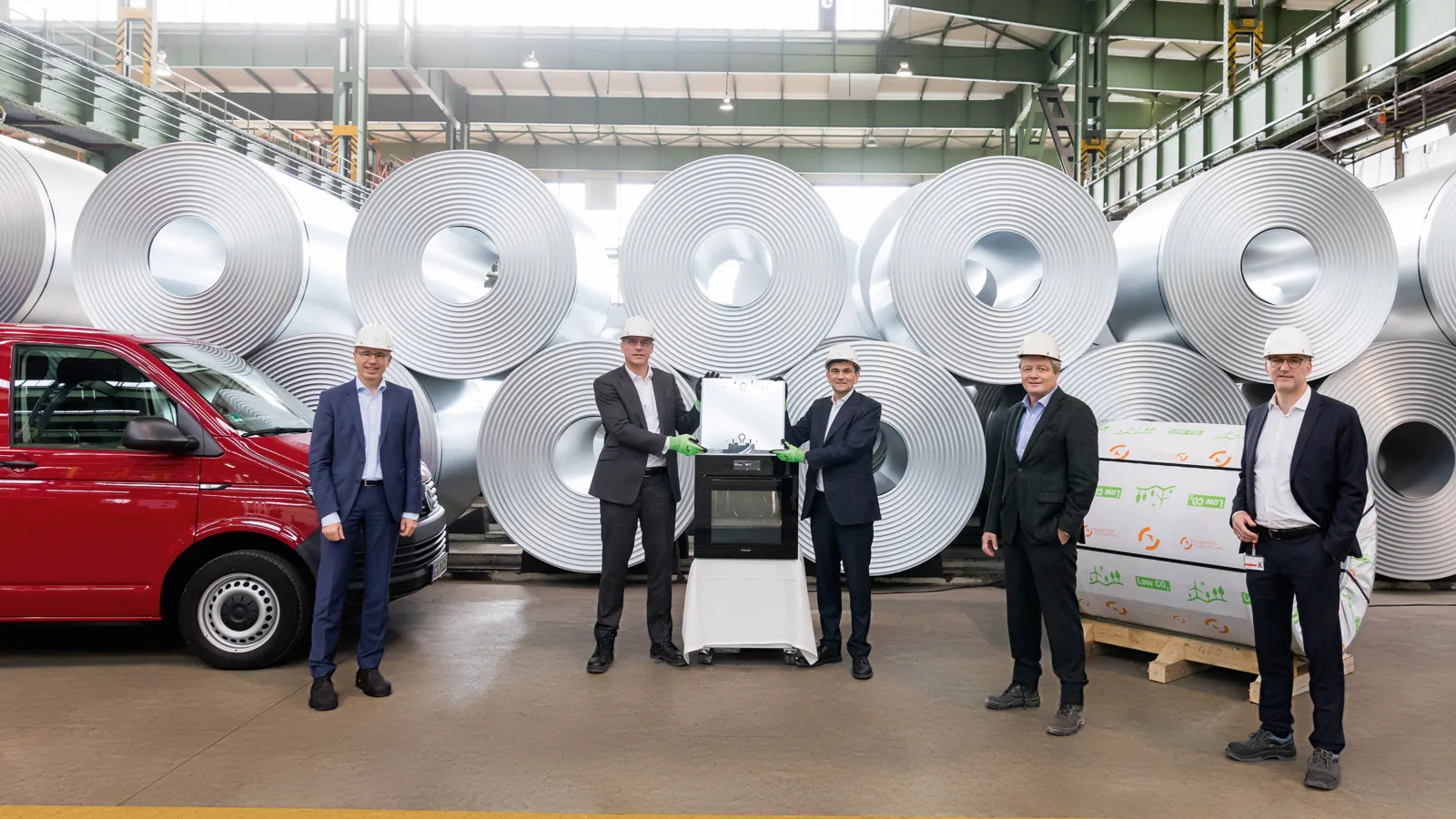
Green milestone
With the manufacture of green strip steel Salzgitter AG is getting one big step closer to its target of climate-friendly steel production. Numerous companies are already using this sustainable material for their products.
In order to successively convert the manufacture of steel to low-CO2 methods, Salzgitter has launched a transformation project entitled SALCOS or Salzgitter Low CO2 Steelmaking. The aim is to gradually switch the production of pig iron over to a hydrogen-based manufacturing process.
The green future has begun
The Salzgitter Group is already producing green strip steel: since the fall of 2020 the climate-friendly material has been made at the electric steelworks in Peine and rolled into hot and cold strip in Salzgitter. Compared to conventional production, here the CO2 footprint has been reduced by 66%. This has been certified by two conformity statements presented by TÜV SÜD to Salzgitter AG in February 2021 – incidentally the first European steel manufacturer to receive such certification. The statements were issued according to the VERIsteel procedure that validates product-specific CO2 emissions for steel production.
Certified green strip steel is eliciting keen interest from a number of companies in various sectors. They believe it is important to start procuring materials now that are produced with a smaller carbon footprint. Environmentally-friendly steel products can be used for many different purposes, such as vehicle manufacture, construction and industrial applications.
High demand
Since July 2021 subsidiary Salzgitter Flachstahl has been supplying its green products to four German Mercedes-Benz plants in Germany, for instance. The CO2-reduced steel rolled into different grades is used in serial production for structural and body parts in various car models.
Another example customer is BSH Hausgeräte, Europe’s largest domestic appliance manufacturer. The company is utilizing the climate-friendly product to forge ahead with the decarbonization of its value chain. At its Polish plant in Lodz green strip steel from Salzgitter is used to make mounting brackets in the production of washing machines.
As part of a pilot project, BSH competitor Miele is also sourcing just under 24 metric tons of low-CO2 steel from Salzgitter a month for the manufacture of its stoves and ovens.
“With our deliveries of CO2-reduced strip steel we’re implementing a key component in our decarbonization strategy,” says Gunnar Groebler, CEO of Salzgitter AG. “We’re consistently pursuing our path towards climate-friendly production with SALCOS. This is a fundamental transformation that will enable us to completely replace conventional steel production in a series of defined steps in favor of hydrogen-based processes. In this way we want to cut our carbon emissions in steel production by over 95%, thus avoiding around 1% of Germany’s current emissions.”